تعد منتجات رغوة البولي يوريثان نوعًا من منتجات البوليمرات المستخدمة على نطاق واسع في البناء والنقل والإلكترونيات والأجهزة الكهربائية والمجالات الطبية وغيرها من الحقول ، وتنقسم عملية الإنتاج بشكل أساسي إلى خطوتين: الرغوة والقولبة. في عملية الرغوة ، يتم التحكم في نسبة ومعالجة المواد الخام مثل البوليمر ، المحفز ، عامل النفخ ، ومثبتة لإنتاج تفاعل كيميائي في الخليط ، مما يؤدي إلى عدد كبير من الفقاعات وأخيراً تشكيل بنية رغوة. في عملية القولبة ، تتم معالجة الرغوة عن طريق القطع والبثق والضغط لصنع أشكال مختلفة من المنتجات. في هذه المقالة ، سنقدم عملية جعل منتجات رغوة البولي يوريثان ومناطق تطبيقها بالتفصيل.
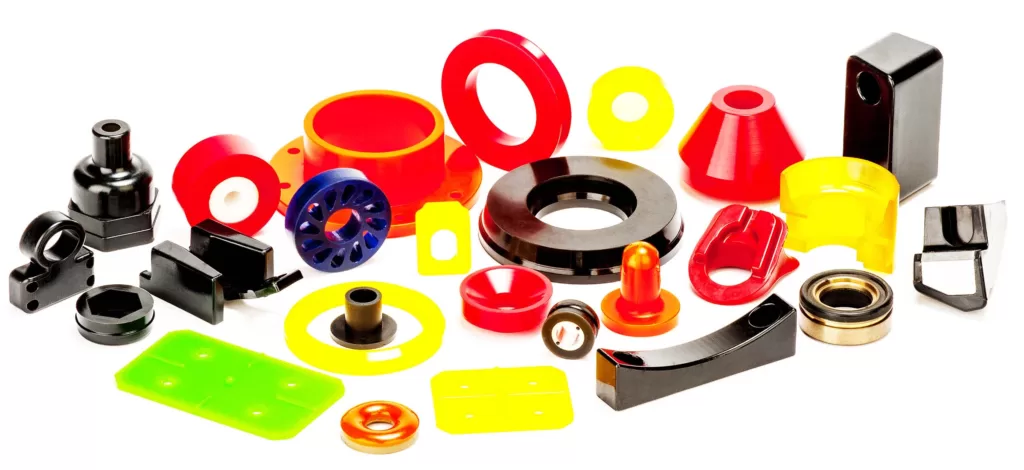
نظرة عامة على منتجات رغوة البولي يوريثان
منتجات رغوة البولي يوريثان هي نوع من منتجات المواد البوليمرية المكونة من عوامل رغوة البولي يوريثان ، والمثبتات ، والمحفزات ، والمواد الحشو ، والمواد الخام الأخرى. إن بنية الرغوة المصنوعة منها لها خصائص ممتازة مثل الوزن الخفيف ، والقوة العالية ، والحفاظ على الحرارة ، وعزل الحرارة ، وامتصاص الصوت ، ومقاومة الصدمات ، ومقاومة التآكل الكيميائي. يستخدم على نطاق واسع في البناء والنقل والإلكترونيات والأجهزة الكهربائية والمجالات الطبية وغيرها. تحتوي مقاعد سيارتنا الشائعة والأثاث ومواد عزل الأنابيب على شكل رغوة البولي يوريثان.
تنقسم رغوة البولي يوريثان بشكل رئيسي إلى فئتين: رغوة صلبة ورغوة ناعمة. تحتوي الرغوة الصلبة على خصائص القوة العالية ، ومقاومة الضغط ، والحفاظ على الحرارة ، وعزل الحرارة ، وتستخدم عادة في جدران البناء ، والأسطح ، والأرضيات ، وألواح العزل ، وألواح التخزين البارد ، وغيرها من الحقول. تحتوي الرغوة الناعمة على امتصاص جيد للصوت ، وحماية الصدمات ، وحماية التعبئة والتغليف ، وغيرها من الخصائص ، وتستخدم عادة في السيارات والطيران والأجهزة الإلكترونية والأثاث وغيرها من الحقول.
يتمثل مبدأ صنع منتجات رغوة البولي يوريثان في التحكم في نسبة المواد الخام وظروف المعالجة بحيث ينتج الخليط تفاعلًا كيميائيًا ، مما يولد عددًا كبيرًا من الفقاعات وأخيراً تشكيل بنية رغوة. تشمل المواد الخام في عملية الرغوة البوليمرات والمحفزات وعوامل الرغوة والمثبتات. البوليمر هو الهيكل الرئيسي لمنتج الرغوة ، ويستخدم المحفز للتحكم في سرعة الرغوة ، وينتج عامل النفخ فقاعات ، ويمنع التثبيت الفقاعات من كسر.
بشكل عام ، تعد منتجات رغوة البولي يوريثان نوعًا من منتج البوليمرات عالي الأداء ومتعدد الوظائف مع آفاق تطبيق واسعة.
مواد
تتكون مادة منتجات رغوة البولي يوريثان بشكل أساسي من جزأين: مادة البولي يوريثان الخام وعامل الرغوة.
مواد البولي يوريثان الخام
- بولي يوريثان من نوع polyether: يستخدم بشكل أساسي لصنع رغوة ناعمة ، مع النعومة الأفضل ، والمرونة ، ومقاومة الماء ، ومقاومة التآكل ، ومناسبة لمقاعد السيارة والأثاث وغيرها من الحقول.
- البوليستر البولي يوريثان: يستخدم بشكل أساسي لصنع رغوة صلبة ، مع قوة عالية ، صلابة ، ومقاومة للضغط ، مناسبة للبناء ولوحة التخزين الباردة والكرتون المبرد وغيرها من الحقول.
- البولي يوريثان من نوع البوليول: يستخدم بشكل أساسي لصنع المطاطية ، مع مقاومة تآكل أفضل ومقاومة للزيت ، ومناسبة للسيارات ، ونقل السكك الحديدية ، والطيران ، وغيرها من الحقول.
وكيل الرغوة
- عوامل النفخ المادي: مثل الفريون ، تستخدم لتشكيل الرغوة عن طريق ضغط الضغط والاسترخاء لنشر الغاز وإذابة الغاز في المادة الخام للبولي يوريثان.
- عوامل النفخ الكيميائي: مثل الماء والإيزوسيانات ، هي عوامل نفخ كيميائية تضاف إلى المواد الخام للبولي يوريثان ، والتي تطلق الغاز من خلال تفاعل كيميائي ، وبالتالي تشكيل رغوة.
بالإضافة إلى المواد الخام للبولي يوريثان وعوامل النفخ ، والمواد المساعدة الأخرى مثل المحفزات والمثبتات والأصباغ. تضاف لجعل منتجات رغوة البولي يوريثان. يمكن لهذه المواد المساعدة تحسين أداء ومظهر الرغوة وضمان جودة المنتجات.
عمل التحضير
يتطلب صنع منتجات رغوة البولي يوريثان تحضيرًا شاملاً لضمان جودة المنتجات وسلامة الإنتاج.
- التنظيف: قبل صنعه ، تحتاج إلى التأكد من أن بيئة العمل والمعدات نظيفة لتجنب تأثير الغبار والشحوم والشوائب الأخرى على المنتجات. ، تحتاج إلى تنظيف المعدات مثل آلة الرغوة ، وخلط الرأس ، والأنابيب للتأكد من عدم وجود بقايا ومن انسداد للاستفادة الكاملة من أداء المعدات.
- تحقق من المعدات: تحتاج إلى التحقق من أداء وحالة العمل لآلة الرغوة ، ومضخة القياس ، ورأس الخلط ، والأنابيب ، وغيرها من المعدات. ، تحتاج إلى التحقق مما إذا كانت درجة الحرارة والضغط ومعدل التدفق والمعلمات الأخرى لآلة الرغوة أمرًا طبيعيًا للتأكد من أن الجهاز يمكن أن يعمل بشكل ثابت وأن جودة المنتجات تلبي المتطلبات.
- التهوية: ستطلق عملية الرغوة البولي يوريثان الرائحة والغاز الضار ، والتي سيكون لها تأثير معين على صحة المشغلين. لذلك ، من الضروري التهوية بالكامل قبل صنع منتجات رغوة البولي يوريثان لطرد الغازات الضارة من منطقة العمل لضمان صحة وسلامة المشغلين.
- التحقق من المواد الخام: قبل صنع ، من الضروري التحقق مما إذا كانت جودة المواد الخام وأداء المواد الخام تلبي المتطلبات. يجب فحص نوع ونسبة وجودة المواد الخام للبولي يوريثان وعوامل الرغوة لضمان أداء وجودة المنتجات.
- معالجة العفن الفارغة: يجب معالجة القالب لضمان أن يكون سطح القالب ناعمًا وخاليًا من الشوائب والغبار. على وجه الخصوص ، يجب تطبيق عامل إطلاق القالب على سطح القالب لتجنب المنتجات التي تلتصق بالقالب ولضمان مظهر وجودة المنتجات.
تدفق العملية
هناك العديد من التفاصيل في صنع منتجات رغوة البولي يوريثان ، ولكن يمكن تقسيم العملية الكلية إلى الخطوات الخمس التالية:
- تحضير القوالب: أولاً ، قم بإعداد قوالب منتجات رغوة البولي يوريثان ليتم صنعها. تأكد من أن سطح القالب سلس وخالي من الشوائب والغبار ، وتطبيق عامل إطلاق القالب على سطح القالب لتجنب المنتجات من التمسك بالقالب.
- مواد الخلط: بعد ذلك ، ضع المواد الخام للبولي يوريثان وعامل الرغوة في رأس الخلط بنسبة معينة وخلطها تمامًا. تجدر الإشارة إلى أن المعلمات مثل وقت الخلط والنسبة ودرجة الحرارة يجب تعديلها وفقًا للمواد والمعدات المحددة لضمان خلط موحد وجودة مستقرة.
- الرش: يتم رش سائل رغوة البولي يوريثان المختلط في القالب ويترك لتوسيع وعلاج بشكل طبيعي. تجدر الإشارة إلى أن سرعة الرش وسمك سائل رغوة البولي يوريثان يجب التحكم فيها عند الرش لتجنب الأسطح غير المستوية وعدم كفاية الرغوة للمنتجات.
- الموضع والمعالجة: يتم وضع منتجات رغوة البولي يوريثان النهائية في بيئة جيدة التهوية وتترك لعلاجها بشكل طبيعي. تجدر الإشارة إلى أن وقت المعالجة ودرجة حرارة منتجات رغوة البولي يوريثان يجب تعديلها وفقًا للمواد والمنتجات المحددة لضمان المعالجة الكافية والجودة المستقرة.
- بعد العلاج: بعد المعالجة ، يجب أن تكون منتجات رغوة البولي يوريثان بعد المعالجة ، بما في ذلك القطع والطحن والرش. تجدر الإشارة إلى أنه يجب تعديل عملية ما بعد العلاج وفقًا لحجم المنتجات والشكل واستخدامها لضمان تلبية ظهور وجودة المنتجات في المتطلبات.
كما ذكر أعلاه ، فإن عملية صنع منتجات رغوة البولي يوريثان بسيطة نسبيًا ، بما في ذلك إعداد القوالب ، ومواد الخلط ، والرش ، والمعالجة ، وما بعد المعالجة. تجدر الإشارة إلى أن نسبة الخلط وسرعة الرش تحتاج إلى التحكم الصارم أثناء عملية الإنتاج لضمان جودة المنتجات واستقرارها.
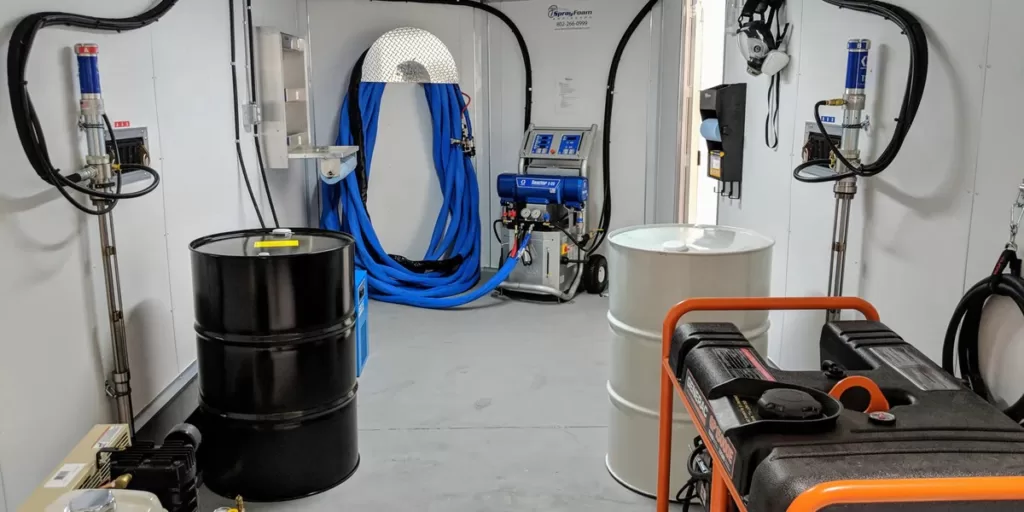
علاج الوقت
إن وقت المعالجة لمنتج رغوة البولي يوريثان هو الوقت المطلوب من الوقت الذي يتم فيه خلط المادة حتى يتم علاج المنتج بالكامل ومستقر. عادةً ما يختلف وقت المعالجة لمنتجات رغوة البولي يوريثان من بضع ساعات إلى عدة أيام.
يعتمد عامل وقت العلاج المحدد على مجموعة متنوعة من العوامل ، بما في ذلك نوع ونسبة المواد المختلطة ، ودرجة الحرارة المحيطة والرطوبة ، وحجم القالب وشكله ، وسمك المنتج. بشكل عام ، ستعمل درجة الحرارة والرطوبة المحيطة الأعلى على تسريع عملية علاج منتجات الرغوة البولي يوريثان ، في حين أن درجة الحرارة والرطوبة المحيطة المنخفضة ستطول وقت المعالجة.
بالإضافة إلى ذلك ، يتأثر وقت المعالجة لمنتجات رغوة البولي يوريثان أيضًا بسمك وشكل المنتج. ستستغرق العلاج أكثر سمكًا أو أكثر تعقيدًا للعلاج لأن رغوة البولي يوريثان تتطلب المزيد من الوقت للعلاج بالكامل.
من المهم أن نلاحظ أن وقت المعالجة لمنتجات رغوة البولي يوريثان قد يؤثر على جدول الإنتاج ووقت الاستخدام ، لذلك عند جعل منتجات رغوة البولي يوريثان ، يجب أن يتم النظر في وقت المعالجة وتخطيطه بالكامل لضمان علاج المنتجات بالكامل وتلبية المتطلبات.
رقابة جودة
يعد التحكم في جودة منتجات رغوة البولي يوريثان أمرًا مهمًا للغاية ويمكن التحكم فيه وضمانه من خلال التدابير التالية وهي ضرورية ولكن ليس كلها:
- مراقبة الجودة للمواد: حدد المواد الخام عالية الجودة وتأكد من أن كل مجموعة من المواد الخام تلبي المعايير المطلوبة. يجب اختبار المواد الخام بانتظام ، وتشمل عناصر الاختبار الكثافة واللزوجة وقيمة الرقم الهيدروجيني وما إلى ذلك.
- صيانة المعدات: تحقق بانتظام من أداء وحالة المعدات لضمان التشغيل العادي. الصيانة المنتظمة وصيانة المعدات ، بما في ذلك التنظيف ، والتشحيم ، واستبدال الأجزاء ، وهلم جرا.
- التحكم في إجراءات التشغيل: توحيد إدارة عملية الإنتاج وتوفير التدريب على المهارات المهنية للمشغلين لضمان أن تكون إجراءات التشغيل صحيحة وموحدة وقابلة للتشغيل.
- فحص الجودة: فحص جودة منتجات رغوة البولي يوريثان ، بما في ذلك المظهر والكثافة والقوة وامتصاص الماء والجوانب الأخرى. التخلص من المنتجات غير المؤهلة ، وتحليل الأسباب وتحسينها.
- الرقابة البيئية: يجب أن تبقى ورشة الإنتاج لصنع منتجات رغوة البولي يوريثان جافة وذات تهوية جيدة ، والحفاظ على درجة حرارة معينة ورطوبة. تجنب الغبار والشوائب وغيرها من الملوثات من دخول ورشة الإنتاج.
مجالات التطبيق
البناء والبنية التحتية
تستخدم منتجات رغوة البولي يوريثان على نطاق واسع في قطاع البناء لعزل الحرارة ، وعزل الصوت ، ومباني العزل المائي. على سبيل المثال ، يتم استخدام صفائح رغوة البولي يوريثان عادة للأسطح العازلة والجدران الخارجية. بالإضافة إلى ذلك ، تعمل مواد ملء رغوة البولي يوريثان بمثابة مانعات فعالة للأبواب والنوافذ.
الفضاء والنقل
تجد صناعة الطيران تطبيقات متعددة لمنتجات رغوة البولي يوريثان. تُستخدم هذه المنتجات لإنشاء مواد عزل حرارة المركبة الفضائية ، ومنصات مضادة للهواء ، وأكثر من ذلك. في قطاع النقل ، تلعب رغوة البولي يوريثان دورًا محوريًا في عزل الصوت وتخميد الاهتزاز للمركبات مثل السيارات والقطارات والطائرات. على سبيل المثال ، يمكن لسائد مقعد السيارة وبطانات السقف المصنوعة من رغوة البولي يوريثان تخفيف الضوضاء والاهتزاز داخل السيارة ، مما يعزز راحة الركوب بشكل عام.
البيئة والحفاظ على الطاقة
تساهم منتجات رغوة البولي يوريثان بشكل كبير في الحفاظ على الطاقة. على سبيل المثال ، يمكن أن تقلل ألواح عزل رغوة البولي يوريثان بشكل كبير من استهلاك الطاقة في المبنى ، مما يؤدي إلى انخفاض فواتير الطاقة وتقليل انبعاثات الكربون. في عالم حماية البيئة ، يمكن لأكياس رغوة البولي يوريثان للتغليف تقليل التلوث البيئي. علاوة على ذلك ، يمكن أن تساعد لوحات عزل صوت الرغوة البولي يوريثان في الحد من تلوث الضوضاء.
المشاكل والحلول الشائعة في الإنتاج
ستحدث المشاكل دائمًا حتماً ، والمبلغ الرئيسي هو ما يلي:
- جودة الرغوة غير المستوية: قد تكون نسبة الخلط غير صحيحة ، ويجب ضبط نسبة المواد الخام. من الممكن أيضًا أن يكون الرش موحدًا ، ويحتاج إلى ضبط الزاوية ومسافة الرش.
- انكماش الرغوة: عادة ما يكون ذلك بسبب انخفاض درجة الحرارة المحيطة أو خلط غير متساو للمواد الخام. يمكن حلها عن طريق رفع درجة الحرارة المحيطة أو إعادة خلط المواد.
- الرغوة غير الكافية أو الصلبة: قد تكون صلابة غير كافية بسبب عدم كفاية نسبة المواد الخام أو الخلط غير المتكافئ ، وقد تكون صلبة للغاية بسبب نسبة مفرطة من المواد الخام أو وقت المعالجة الطويل للرغوة. تحتاج إلى إعادة ضبط النسبة أو التحكم في وقت المعالجة.
- تكسير الرغوة: قد يكون ذلك بسبب الرش الكثيف للغاية أو الرطوبة العالية في البيئة ، مما يؤدي إلى معالجة الرغوة غير المستوية. تحتاج إلى التحكم في سمك الرش والرطوبة.
- تلون الرغوة أو الأكسدة: قد يكون ذلك بسبب المواد الخام ليست جديدة أو مخزنة لفترة طويلة جدًا ، وتحتاج إلى استبدال المواد الخام الجديدة أو تعزيز إدارة التخزين.
لمعالجة هذه المشكلات ، يمكن اتخاذ التدابير التالية:
- التحكم الصارم في جودة المواد الخام ونسبة التناسب لضمان خلط موحد.
- تحسين صيانة وإصلاح المعدات لضمان جودة واستقرار الرش.
- تحكم في درجة حرارة ورطوبة البيئة لضمان توحيد علاج الرغوة.
- تعزيز إدارة موقع الإنتاج لمنع الخسارة الناجمة عن تشغيل غير لائق أو مشاكل الجودة.
يجب التحكم في الإنتاج بصرامة في جميع المراحل لضمان جودة مستقرة. في الوقت نفسه ، يجب حل المشكلات التي قد تنشأ أثناء عملية الإنتاج في الوقت المناسب لضمان جودة المنتجات وكفاءة الإنتاج.
الاحتياطات عند الإنتاج
البولي يوريثان هو نوع من المجمع الكيميائي. خلال عملية إنتاج منتجات البولي يوريثان ، سيتم تنبعث المواد الضارة. لذلك ، يجب أن تضع المؤسسات السلامة أولاً.
- السلامة أولاً: أثناء عملية الإنتاج ، انتبه إلى الوقاية من الحرائق والوقاية من الانفجار ، وحماية نفسك والأشخاص من حولك.
- التهوية: سيتم إنشاء الغازات الضارة أثناء إنتاج منتجات رغوة البولي يوريثان ، لذلك يجب اختيار مكان جيد التهوية للإنتاج ، ويجب ضمان تداول الهواء.
- صيانة المعدات: تحقق بانتظام من المعدات والحفاظ عليها ، والحفاظ على نظافة المعدات ، وتجنب الشوائب من الخلط في مواد.
- تخزين المواد: يجب تخزين مواد البولي يوريثان في مكان جاف وبارد وتهوية ، وتجنب أشعة الشمس المباشرة ودرجات حرارة عالية.
- نسبة الخلط: عند خلط المواد الخام للبولي يوريثان ، من الضروري التحكم بدقة في نسبة الخلط ، وإلا فإنه سيؤثر على أداء المنتج وجودة المنتج.
- وضع العفن: قبل سكب المواد الخام البولي يوريثان المختلطة في القالب ، من الضروري وضع القالب في الموضع الصحيح والتأكد من أن السطح الداخلي للقالب نظيف.
- متطلبات حماية البيئة: يحتاج إنتاج منتجات رغوة البولي يوريثان إلى تلبية متطلبات حماية البيئة لتقليل توليد النفايات والمواد الضارة.
احتمال السوق
يقع سوق منتجات Polyurethane Foam حاليًا في مرحلة من التطوير السريع ، ويستمر مقياس السوق العالمي في التوسع. مع مراعاة مجال البناء كمثال ، تستخدم منتجات الرغوة البولي يوريثان بشكل أساسي في جدران البناء ، والأسطح ، والأرضيات ، والأنابيب ، والتخزين البارد ، وغيرها من الحقول ، ولها خصائص ممتازة مثل عزل الحرارة ، والحفاظ على الحرارة ، والوقاية من الحرائق ، ومقاومة الرطوبة ، وعزل الصوت. وفقًا لبيانات وكالات أبحاث السوق ، بلغ سوق منتجات الرغوة البولي يوريثين العالمية 12.5 مليار دولار أمريكي في عام 2019 ، ومن المتوقع أن ينمو إلى 18 مليار دولار بحلول عام 2025 ، مع معدل نمو سنوي مركب قدره 5.5 ٪.
في مجال السيارات ، تستخدم منتجات رغوة البولي يوريثان أيضًا على نطاق واسع في عزل الصوت ، وامتصاص الصدمات ، والحفاظ على الحرارة ، وجوانب أخرى من السيارة. مع ظهور مركبات الطاقة الجديدة وتعزيز اتجاهات السيارات الخفيفة ، ستكون آفاق منتجات رغوة البولي يوريثان أوسع.
بالإضافة إلى ذلك ، مع تحسين الوعي بالحفاظ على الطاقة وحماية البيئة ، فإن تطبيق منتجات رغوة البولي يوريثان في المباني الموفرة للطاقة ، والفضاء ، والإلكترونيات ، والأجهزة المنزلية ، وغيرها من المجالات يتوسع تدريجياً. يمكن التنبؤ بأن يستمر احتمال سوق منتجات الرغوة البولي يوريثان في الحفاظ على زخم جيد للتنمية.
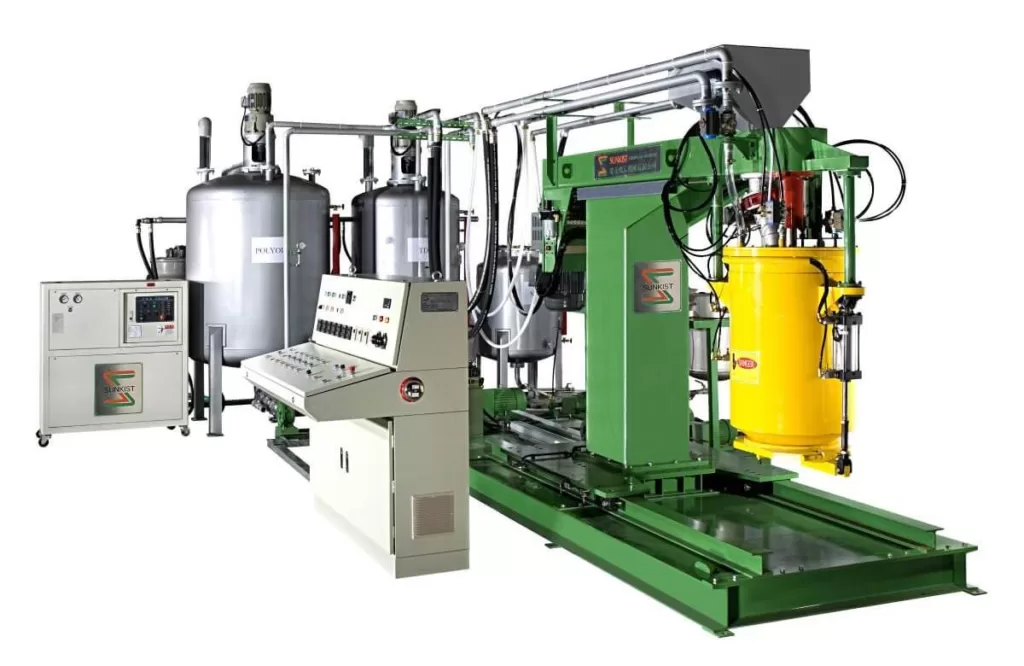
خاتمة
إن فهم العملية المعقدة وراء إنتاج رغوة البولي يوريثان يلقي الضوء على الجهود الدقيقة والدقة اللازمة لإنشاء هذه المنتجات متعددة الاستخدامات. مع استمرار التطور الصناعي ، يكون الطلب على هذه المواد القابلة للتكيف واضحًا. من خلال استيعاب الفروق الدقيقة في إنتاجها ، يمكننا أن نقدر قيمة وإمكانات البولي يوريثان بشكل أفضل في تشكيل عالمنا الحديث.